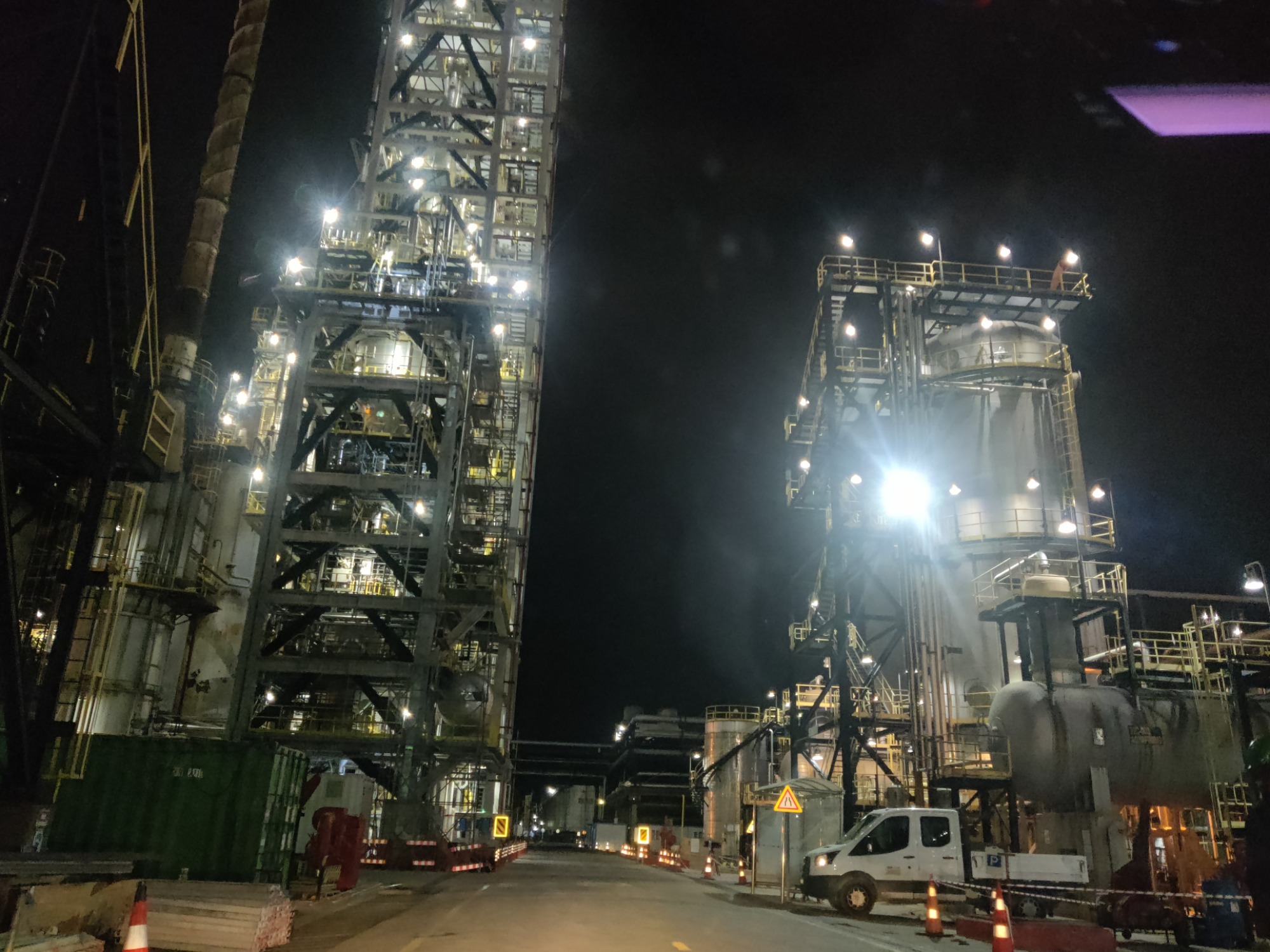
Boilers in petrochemical plants are essential for generating steam, hot water, and process heat. Their proper maintenance is crucial for safe operation, efficiency, and longevity. Here’s a comprehensive guide on the functions, working principles, and maintenance practices for boilers:
1. Functions and Areas of Use
- Steam Generation:
- Purpose: Produce steam for various applications including steam turbines, process heating, and power generation.
- Applications: Used in chemical processes, steam-driven machinery, and as a source of heat for reactions and distillations.
- Hot Water Generation:
- Purpose: Supply hot water for heating systems and industrial processes.
- Applications: Often used in heating systems for buildings or as a component in chemical processes.
- Process Heat:
- Purpose: Provide high-temperature heat necessary for chemical reactions or other processes.
- Applications: Essential for reactors, catalyst activation, and other high-temperature processes.
2. Working Principle
- Fuel Combustion:
- Sources: Boilers can burn various fuels such as natural gas, fuel oil, coal, or biomass.
- Combustion Process: The fuel burns in the combustion chamber, generating heat.
- Heat Transfer:
- Media: Heat is transferred to water or thermal oil circulating in the boiler.
- Circulation: The heat transfer fluid absorbs the generated heat and transfers it to the system.
- Steam Generation:
- Steam Production: Water is converted into steam by heating, which is then used for various applications.
- Control Systems: Automated controls regulate temperature, pressure, and fuel supply to ensure efficient operation.
3. Design and Safety
- Design Considerations:
- Capacity: Boiler design is based on the plant’s capacity needs, fuel type, and process requirements.
- Efficiency: Design includes considerations for efficiency, heat transfer, and emissions control.
- Safety Measures:
- Periodic Checks: Regular inspections and maintenance of pressure parts, safety valves, and fuel systems.
- Automation: Monitoring and control systems to ensure safe operation and automatic shutdown in case of failures.
- Cleaning and Maintenance:
- Scaling: Regular cleaning to prevent scaling and fouling, which can impact efficiency.
- Inspection: Routine checks for leaks, corrosion, and wear.
4. Application Areas
- Industrial Facilities:
- Usage: In large-scale industrial settings like oil refineries and chemical plants for process heating and steam generation.
- Power Generation:
- Usage: To generate steam for turbines in electricity production.
- HVAC Systems:
- Usage: In heating, ventilation, and air conditioning systems for large buildings or industrial facilities.
Maintenance Best Practices
- Regular Inspections:
- Perform routine inspections of the boiler’s components, including pressure parts, fuel systems, and safety devices.
- Preventive Maintenance:
- Schedule regular maintenance tasks such as cleaning, lubrication, and part replacements based on manufacturer recommendations.
- Performance Monitoring:
- Continuously monitor the boiler’s performance through control systems and sensors to detect any deviations or issues early.
- Safety Checks:
- Ensure all safety devices are functional, including pressure relief valves, alarms, and shutdown systems.
- Documentation:
- Keep detailed records of all maintenance activities, inspections, and repairs. This helps in tracking the equipment’s condition and planning future maintenance.
- Training:
- Provide regular training for maintenance personnel on the latest technologies, safety procedures, and maintenance techniques.
Proper boiler maintenance ensures efficient operation, extends the lifespan of the equipment, and maintains safety and compliance with industry standards. By following best practices and adhering to safety guidelines, petrochemical plants can optimize their boiler performance and reliability.