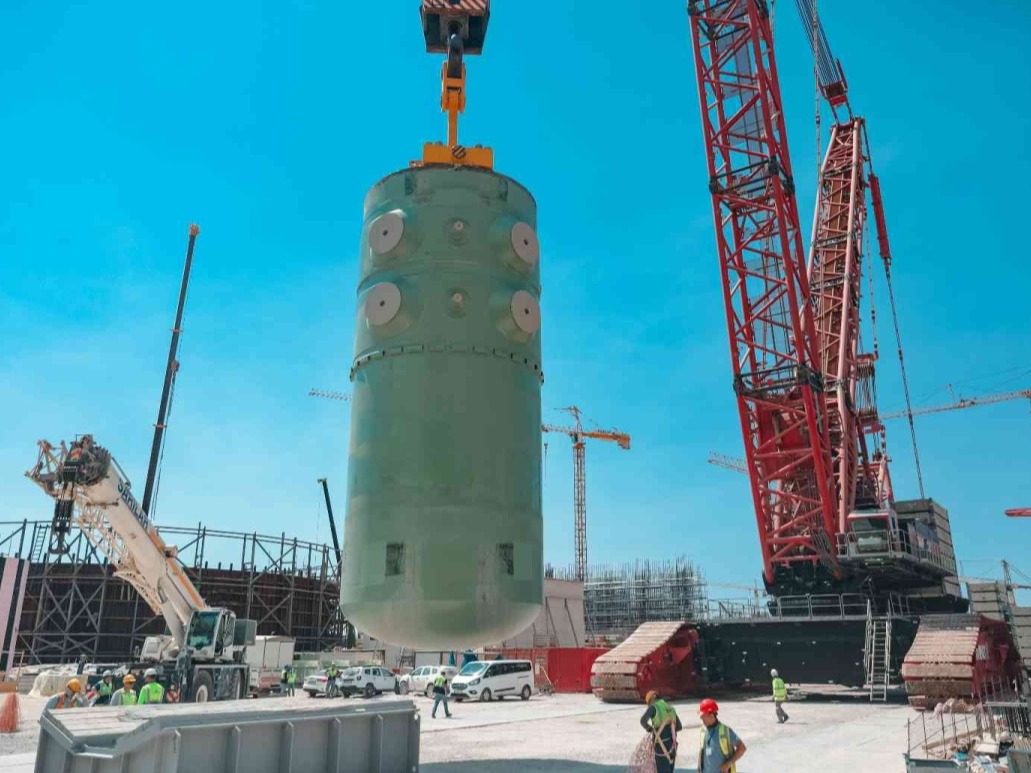
Reactors are essential components in petrochemical & refinery plants, designed to carry out, control, and direct chemical reactions. Their proper maintenance is crucial for ensuring efficient and safe operations. Here's a detailed overview of the reactors commonly used in these facilities:
1. Types and Functions:
- Serial Reactors: These reactors operate in sequence, with the process fluid passing through each reactor in turn. This setup allows optimization of reaction conditions at different stages of the process.
- Parallel Reactors: Used to conduct multiple reactions simultaneously. This design enables the processing of different reactions concurrently, improving overall efficiency.
- Continuous Reactors: Designed for uninterrupted operation, these reactors continuously receive material and provide a constant output. They are ideal for large-scale, ongoing production processes.
- Batch Reactors: Operate in discrete batches where a set quantity of material is processed at a time. After each batch, the reactor is cleaned and refilled for the next cycle.
- High-Pressure Reactors: Capable of operating under elevated pressures, these reactors are used for gas-phase reactions or specialized chemical syntheses that require high-pressure conditions.
- High-Temperature Reactors: Built to withstand high temperatures, these reactors facilitate reactions that require significant thermal processing.
2. Working Principle:
- Reaction Conditions: Chemical reactions in reactors are controlled within specific temperature, pressure, and time ranges. Optimizing these conditions is essential for achieving desired products and minimizing unwanted byproducts.
- Catalysts: Often used in reactors to enhance reaction rates, increase selectivity, or reduce byproduct formation. Catalysts play a critical role in improving reaction efficiency and product quality.
3. Application Areas:
- Petroleum Refineries: Reactors are used to convert various hydrocarbons, such as in catalytic reformers that transform gasoline into aromatic hydrocarbons.
- Chemical Synthesis Plants: Employed to synthesize a wide range of chemical substances, including industrial chemicals, plastics, paints, pharmaceuticals, and other products.
- Gas Processing Plants: Essential for processing natural gas and other gases. For instance, reactors are used to convert methane into methanol or synthetic fuels.
4. Design and Safety:
- Design Considerations: Reactor design depends on process conditions, reaction types, and material properties. Key factors include material selection, sealing mechanisms, and thermal control to ensure efficient and safe operation.
- Safety Measures: Achieved through correct reactor operation, regular maintenance, and comprehensive training for operators. Adhering to safety protocols and conducting periodic inspections are critical for preventing accidents and ensuring operational integrity.
Reactors in petrochemical plants are pivotal for enhancing product diversity, improving process efficiency, and minimizing environmental impacts. Continuous innovation and optimization in reactor design are essential to meet evolving industry needs and maintain high standards of performance and safety.